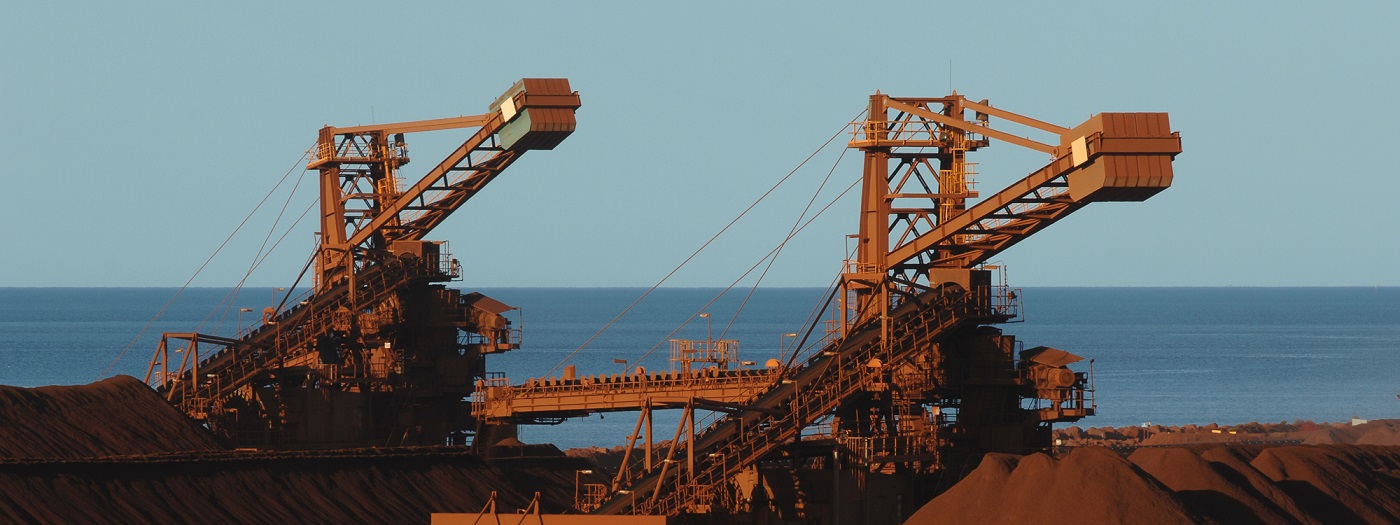
SMEC’s Asset Management team was engaged by one of the world’s largest copper producer to identify potential savings associated with maintenance of equipment at the mine site located in Chile.
Our main objective for this project was to achieve a benchmark maintenance strategy for plant availability, with optimised labour and spare parts inventory. To achieve all the above we had to look at the processes from a very strategic view and holistic approach understanding the key drivers for each area. Then, depending on the area, production line or process, we assessed, using our analytic skills, benchmark information and our methodology, what was the best mixture of maintenance tactics to achieve project goals.
This optimisation exercise, achieved the following results in terms of the project objectives:
How did we achieve these figures?
I am positive it was our methodology that played a fundamental role in achieving these unprecedented results. It was a key factor that enabled us to effectively achieve what the client was looking for, meaning productivity, efficiencies and cost savings.
We designed a maintenance strategy optimising the current maintenance plans, in terms of availability increase (scheduled downtime: frequencies and durations; unplanned downtime based on failure modes analysis), asset integrity coverage (increasing dominant failure modes and components coverage avoiding catastrophic failures), cost reduction in terms of labour and spare parts expenditures and inventory, and increasing the quality of maintenance tasks through task-list with right activities and resources.
The timelines we had to work were extremely tight and we had multiple stakeholders to engage. Our project may not have worked so well if it weren’t for the people involved in it.
Firstly, our client played a key role when they assigned 100% dedicated people to help us push through the project’s milestones. They committed to meetings and workshops and immediately addressed elements we raised that required validation. Their commitment from top stakeholders and dedicated staff supported the project’s success daily. And of course, the SMEC team which was made up of 55 consultants from Chile and Australia. These consultants’ capacity and experience was key to achieve the project targets. The intensity of the project including weekly workshops, totalling 440 throughout the project’s lifecycle with 350 participants, was relentless. It had the potential to be a logistical minefield, but it was easy to navigate due to our structured approach and our people’s relationship building skills.
In terms of the achieved goals, the numbers are unique because the size of the project site is huge compared with other mining sites in the world. That said, we are replicating the methodology across five different projects right now and we’re already seeing an increase of production and reduction in project costs for these smaller projects. In terms of savings and efficiencies, all clients should be demanding these kinds of outcomes from their external advisors.
These kinds of intensive initiatives require lots of involvement not only from the client’s top executives, but also from the advisory side. For us, we had the full commitment from our SMEC leaders which was integral to our ability to support so many consultants across the business.
Related
insights
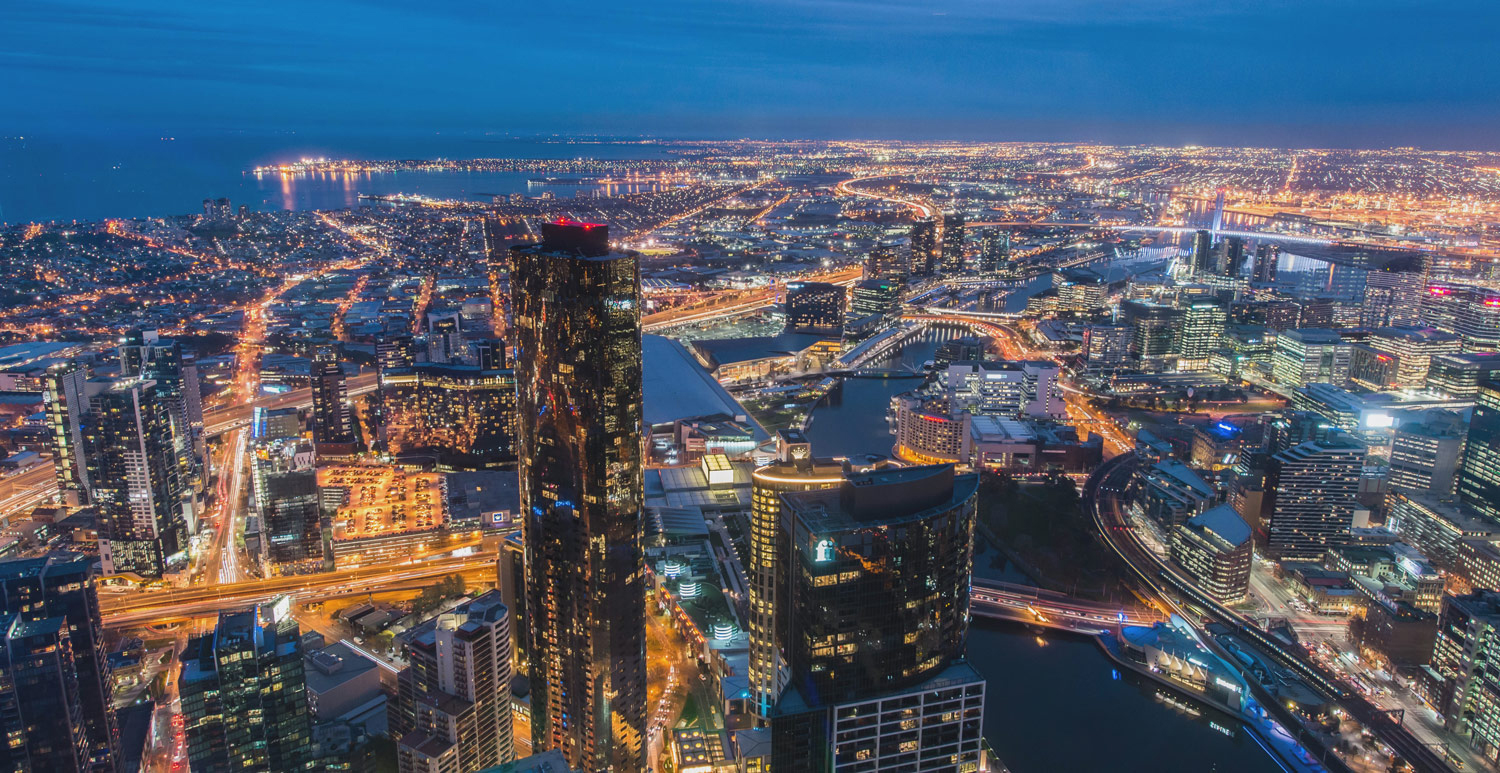
SMEC is made up of problem solvers. We have always helped to find solutions for people - it’s part of our DNA. That’s why the Smart Cities agenda simply represents a contemporary part of our innovation journey and fits neatly into SMEC’s strategic approach to grow and diversify our business.
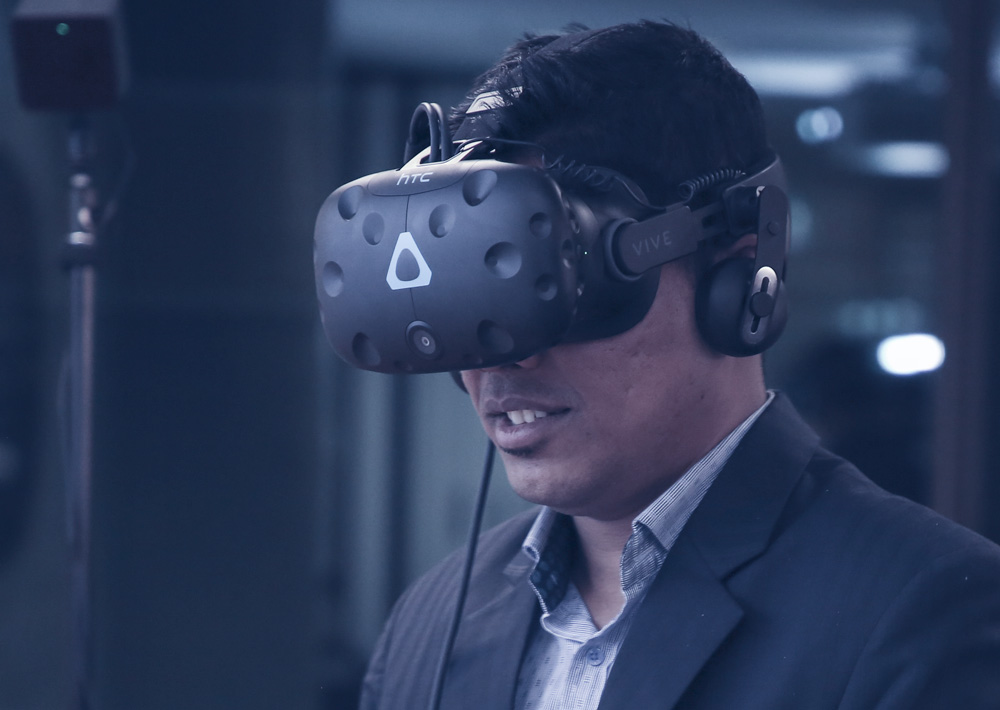
SMEC is collaborating with frontier technology company Snobal, to transform design, enrich stakeholder engagement and deliver innovative solutions for our clients.
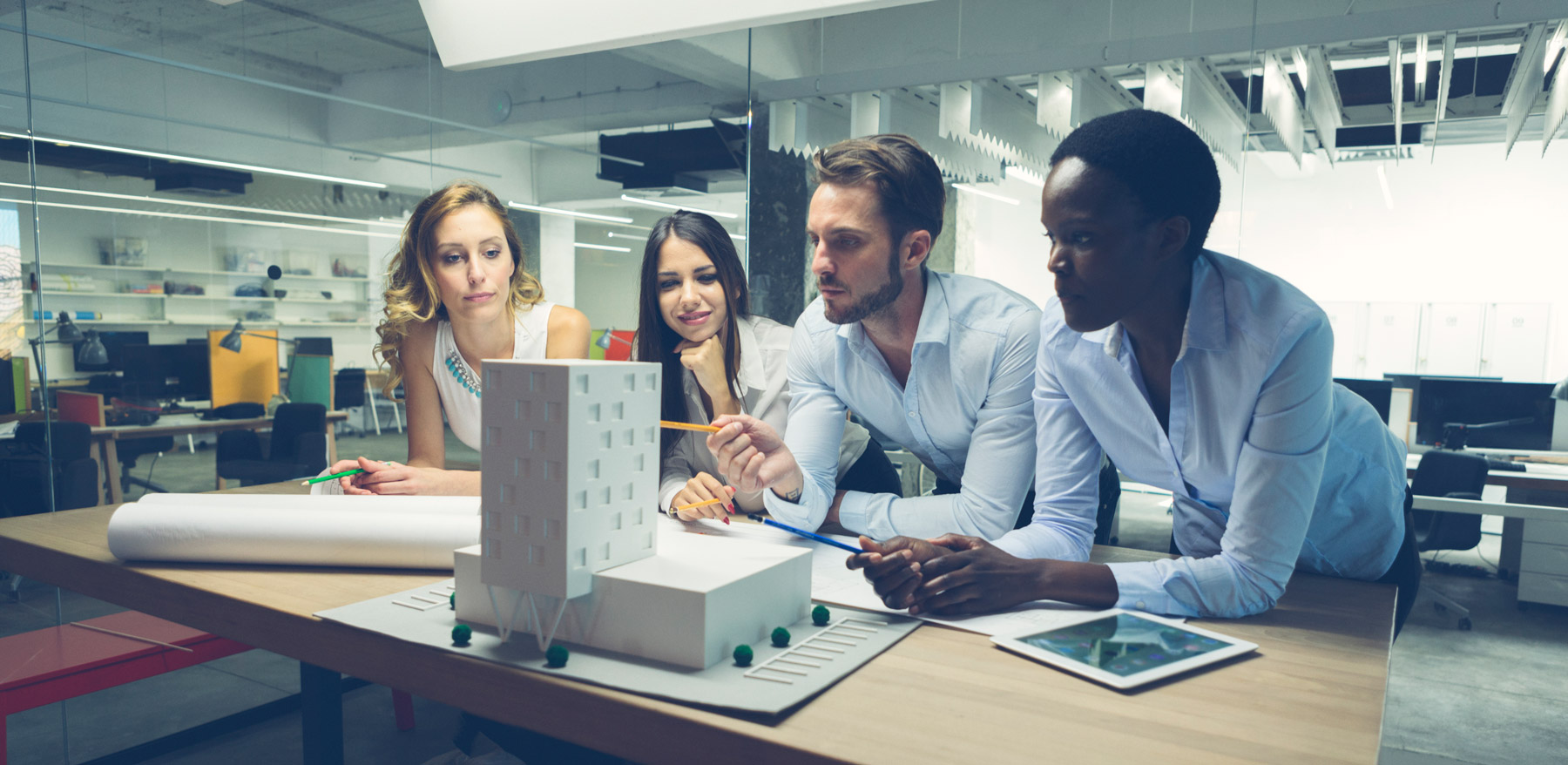
Technology is accelerating the pace of change and disrupting every aspect of modern life. Engineers of the future will face a critical challenge to lead, shape, plan and integrate the built environment solutions that allow society to live safe and rewarding lives. Aaron Foong explains why.

Australia is in the midst of a significant energy transformation. It’s estimated that by 2040 the vast majority of Australia’s coal-fired power stations will have been retired, and the nation should be running on 85% renewable energy.