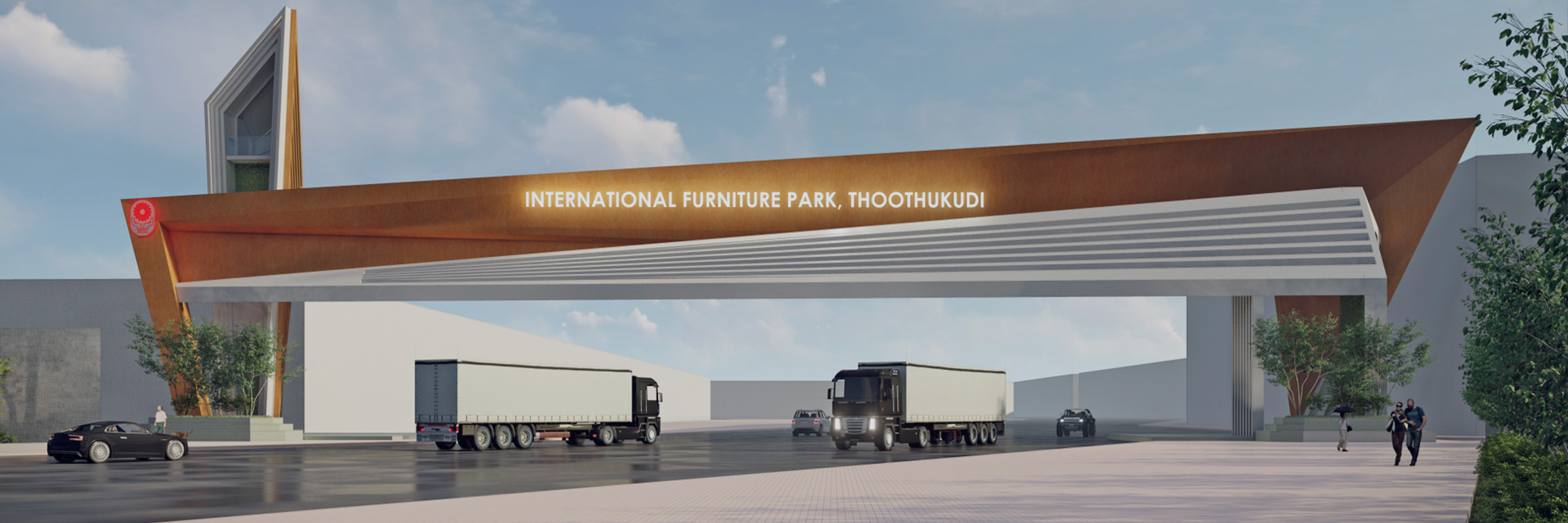





1
st
International Furniture Park in India
465
ha
Land area identified for urban renewal
300000
Projected employment opportunities
Ready
to
connect?
Talk to one of our specialists about the Thoothukudi International Furniture Park project.