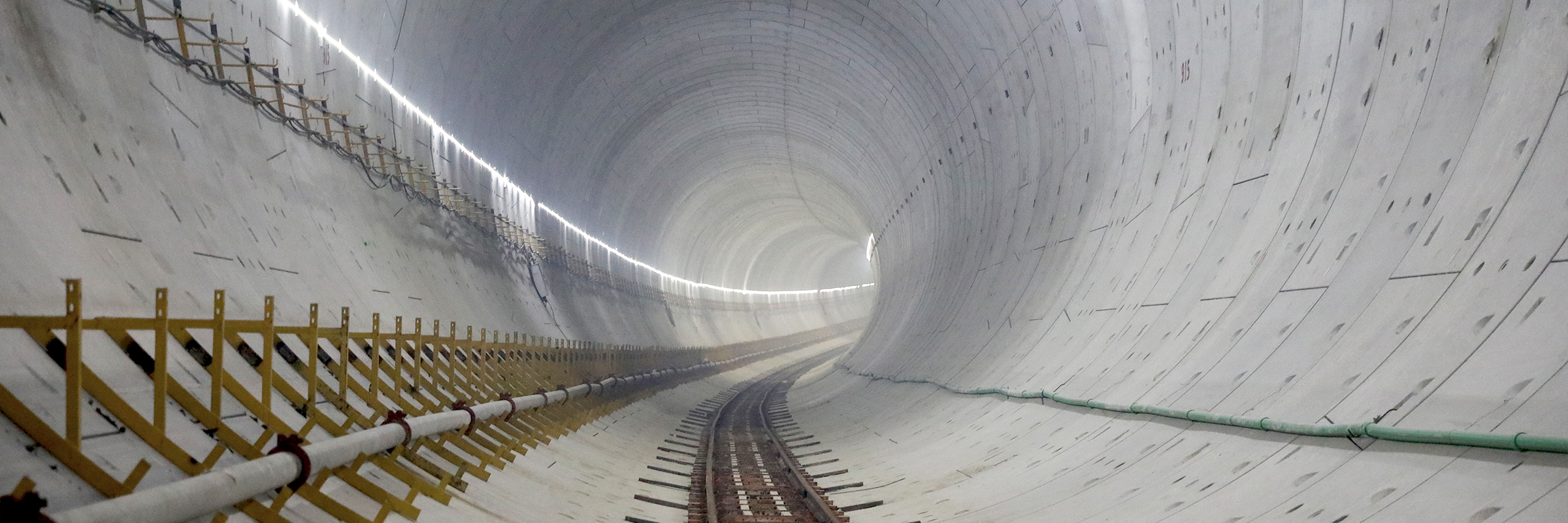
Solution
Tunnel Boring Machine (TBM) and excavation
The tunnel was bored using the slurry shield method. Slurry shields are used for excavation in soils with an unstable tunnel face. The slurry is used to support the tunnel face with pressurized slurry (bentonite suspension) and to allow the installation of segments within the shield body.
The excavation diameter of the shield machine was 12.16 m, the total length of the shield body was 13.58 m, and the total tunnel boring machine length was 95 m, including four gantry sections. Jet grouting around the concrete tunnel wall (called rings) was undertaken to improve soil conditions to prevent ground settlement and prevent leakage into the tunnel. Some issues occurred during the first tunnel excavation that caused the shield to slightly compress. For the second tunnel, the contractor excavated a slightly wider corridor, extending the cutting diameter by 30 mm which gave the TBM more clearance to move forward.
The ARiGATAYA® System was the principal tool used by the contractor for data collection and management of the TBM Tunneling works. It provided real-time data on the TBM’s progress and performance, which helped the team make informed decisions about how to operate the TBM safely and efficiently. The SMEC JV team supported the contractor through the provision of expert advice when driving the TBM. The team also designed a Tunnel Management System, which enabled the team’s tunnelling experts to gather, interrogate, and analyse live data to better inform the owner and contractor of any issues that occurred during tunnelling.
The TBM was assembled and inspected by the owner and SMEC JV team in China and then disassembled and exported from China to Bangladesh’s Chattogram’s port by ocean-going transportation.
Tunnel construction
The tunnel has an internal diameter of 10.8 m made up of eight concrete segments to form the cylinder. Approximately 1,225 precast concrete rings have been installed to line the tunnel, each with a width of 2 m and a thickness of 500 mm.
All segments were manufactured in China and shipped to Bangladesh. The SMEC JV team appointed supervisors to monitor the manufacture and ensure acceptable final quality of each segment prior to shipping. SMEC participated in testing in collaboration with Tongji University, Shanghai to test the installation and watertightness of the EPDM gaskets.
Working shafts with heights of about 38 m were constructed at both ends of the main tunnel. These structures were mostly constructed below ground by bottom-up method. Due to the silty sandy nature of soils in this region, the working shaft, cut and cover, and open cut sections of the tunnel were constructed inside diaphragm walls that prevented the collapse of the soils. The SMEC JV team closely monitored both the lowered water table levels and horizontal ground displacement to ensure adjoining structures were not damaged during construction of the working shafts or cut and cover and open cut sections of the tunnel. The working shafts were initially used for the TBM launching and receiving, and segment installation. Once excavation was completed, they were converted into firefighting and water supply equipment and substation buildings.
Slurry Treatment
The space in front of the TBM cutter head was filled with pressurised slurry composed of bentonite that applied hydrostatic pressure to the soil-face opposite the cutter head. The slurry was mixed with the excavated soil before it was pumped from the cutter head to a slurry treatment plant, located on the surface near to the working shafts. Multi-stage filtration systems were used that separated spoil from slurry to allow reuse of the slurry. Excavated soil was transported from the slurry treatment plant to the reclamation areas utilising an environmentally friendly sediment discharge system. The reclamation areas were closely monitored to ensure no soil or water could escape into the adjoining watercourses.
Tunnel safety features
The tunnel has multiple safety features that protect the tunnel and its users. These include ventilation fans, firefighting hoses and extinguishers, fire alarms, smoke and fire sensors, cross passages, emergency escape slides, monitoring cameras and communication devices placed inside the tunnel for protection of users, and fireproof membranes on the inside roof and upper walls and segment concrete using fibre to protect the tunnel in case of fires.
Three pedestrian cross passages are installed to enable rapid access and evacuation during an emergency. Each cross passage is located approximately 700 m apart. Emergency slides are located every 80 m enabling tunnel users to escape by sliding down into a passageway beneath the road. The cross passages have been constructed using an innovative frozen soil method, which stabilised the ground around the soil during excavation. The SMEC JV team closely monitored this activity to ensure a safe outcome.
The ventilation system consists of 56 ventilation fans that ensure that the air inside is fresh and breathable. The ventilation system is also designed to remove harmful gases and fumes from the tunnel. The fans are activated using traffic, smoke and visibility sensors located throughout the tunnel or through the control centre.
The SMEC JV team also supervised the installation of CCTV cameras within the tunnel which can quickly identify the location and seriousness of a fire or accident, to expedite an emergency response.
Environmental Management
The SMEC JV team oversaw the environmental management component for the whole life of the project, ensuring all works complied fully with both Government regulations and internationally recognised best practice. The tunnel caused minimal ecological impacts and the SMEC JV team implemented strict protocols to monitor the Contractor and achieve compliance.
Environmental management procedures included regular and frequent site inspections and water quality testing to ensure effluent did not find its way into the river system. Noise and air quality was also tested as part of the environmental risk management practices to provide early warning and highlight potential issues with the owner and the contractor before they arose.
Approach Roads and Toll Plaza
Four lane expressway standard approach roads connecting to the tunnel were constructed on both sides of the river. The approach road on the north side of the river connects with the Chattogram outer ring road. It is 550 m long and includes a weigh station for heavy vehicles. The approach road on the south side is 5.4 km long, including a 700 m long viaduct, 400 m long toll plaza and a weigh station for heavy vehicles.
On the approach to the tunnel, the road transitions into an open cut section and then a cut and cover tunnel before descending underground into the tunnel. Rain shelters were constructed on top of each open cut section to minimize rainwater entering the tunnel. Any rainwater still managing to enter, is captured at the portal, and pumped to local drains after treatment. A drainage sump is located at the lowest point in each tunnel to collect any water that comes from ring leakage, cleaning or from firefighting activities. This water is pumped to the surface for treatment prior to release into the local drains. Flood gates have been installed at the portal entrance to prevent any water entering the tunnel in the event of a serious cyclonic storm tidal surge.
The 5.4 km approach road on the south side of the river, included underpasses to ensure safe passage for adjacent communities. A 750 m long viaduct was constructed over a fertiliser factory conveyor. This required the SMEC JV team to work with the owner and the factory management to determine required clearances and other safety features for the viaduct. The SMEC JV team acted as adviser to the owner in all meetings with important stakeholders including Chattogram Development Authority, Bangladesh Bridge Authority, Bangladesh Power Development Board, Bangladesh Navy and the Panel of Experts.
The Toll Plaza is located on the south side of river on the approach road utilising manual and modern automatic toll collection methods. The development of the design of the iconic looking toll collection structure required close coordination of the owner, Contractor and SMEC JV team. The finished structure was met with highly positive feedback from the owner and stakeholder parties. The SMEC JV team provided ongoing design advice during the development of the tolling and overloaded vehicle detection software. Overloaded and oversized vehicles are prevented from entering the tunnel. Each side of the tunnel has overloaded vehicles detectors and oversized barriers. X-ray and under vehicle scanners are also being introduced at both weigh stations to allow early detection of security threats.
Mixed-use Service Area
The project scope included the design and construction of a 38-hectare mixed use service area adjacent to Parki Beach which is about 6 km south of the Karnaphuli River. It will provide accommodation facilities consisting of 30 three-bedroom bungalows and 48 two-bedroom apartments as well as a mosque, health centre, museum, reception building and convention centre. The service area includes recreational zones as well as swimming, tennis, walking tracks and playground areas. It is also near the shoreline, allowing residents to swim and walk along the beach. The SMEC JV team assisted the owner develop the concept design and worked with the contractor to oversee the planning and implementation of the service area.
Testing, Commissioning and Asset Management
The SMEC JV team was a key advocate in the development and management of comprehensive pre-commissioning, commissioning, and trial processes. This was effective in ensuring that all equipment worked in accordance with specifications. Equipment testing encapsulated the communication, monitoring, ventilation, lighting, drainage, power, and firefighting systems – ensuring that they worked collectively, as an integrated system. The sensors within the tunnel were checked to ensure they activated the appropriate system.
Impact
- Approximately 17,000 vehicles per day will travel through the tunnel with capacity to increase to over 28,000 vehicles per day.
- The Bangabandhu Sheikh Mujibur Rahman Tunnel will provide significant economic benefit to Bangladesh by providing the catalyst to expand industrial and tourism areas south of the Karnaphuli River.
- The tunnel will provide a bypass route for Chattogram traffic as well as those travelling from Dhaka bound for the tourist city of Cox’s Bazar. This will reduce their travel times significantly.
- The project is part of the ›One Belt One Road‹ initiative providing a key link in cross-country transport corridors.
- The construction of the Bangabandhu Sheikh Mujibur Rahman Tunnel enabled the training of over 50 local Bangladeshi engineers in tunneling construction and design methods. These newly trained engineers will provide essential support to ongoing tunnel projects in Bangladesh, such as Dhaka Metro.
- The project’s success has given the government confidence in the TBM methodology which is now being deployed on other mega projects, such as Dhaka metro.





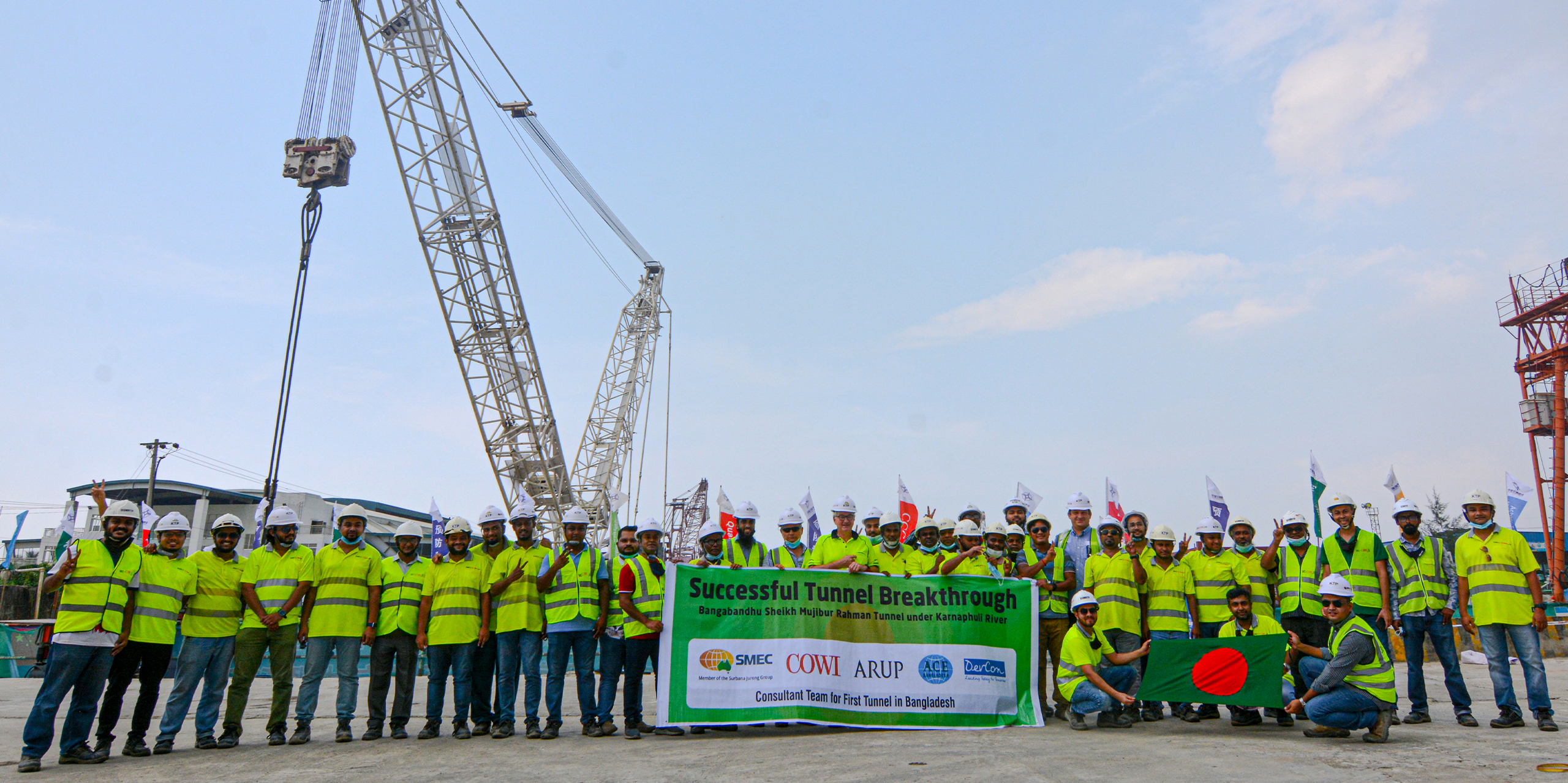





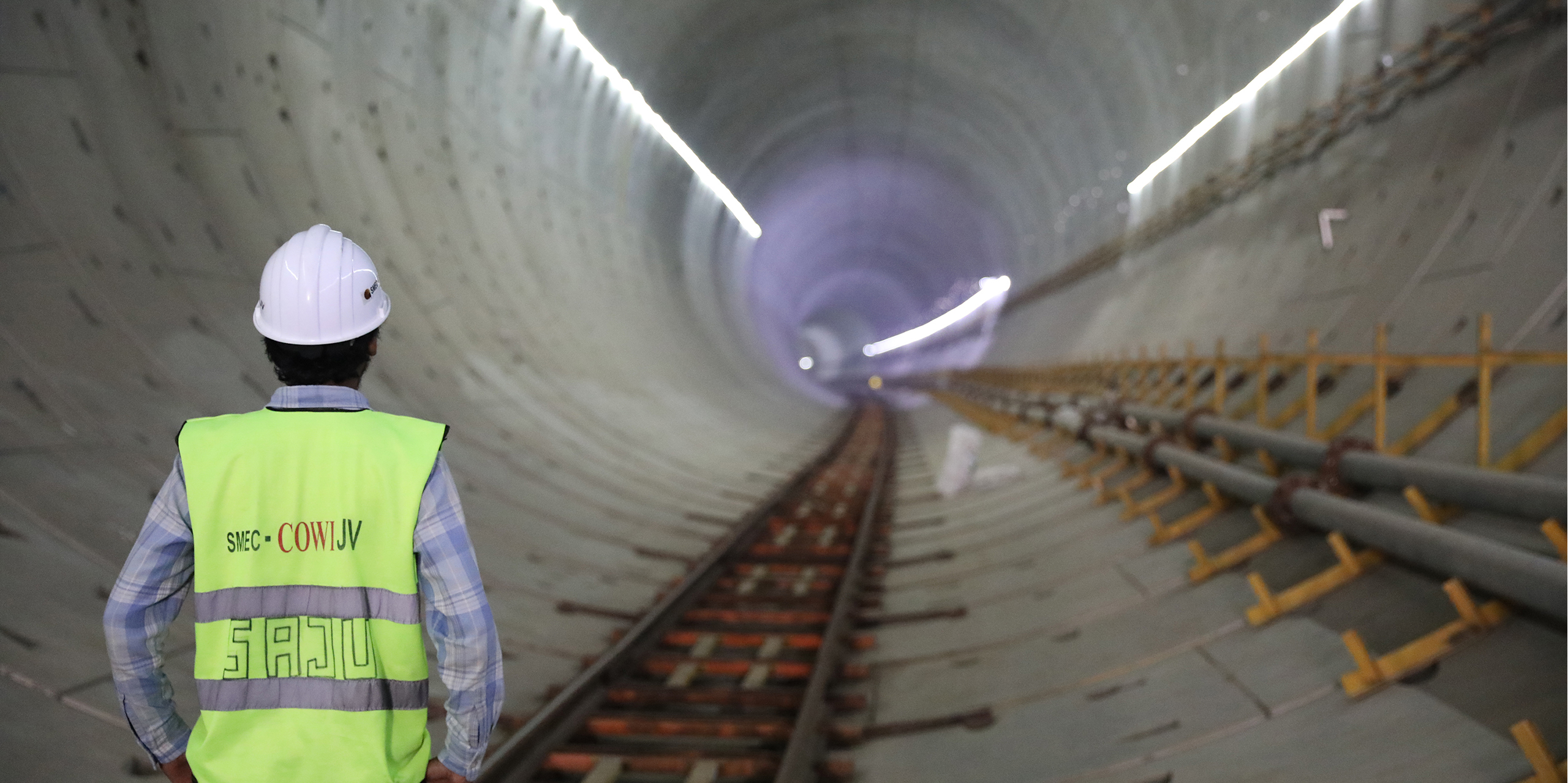
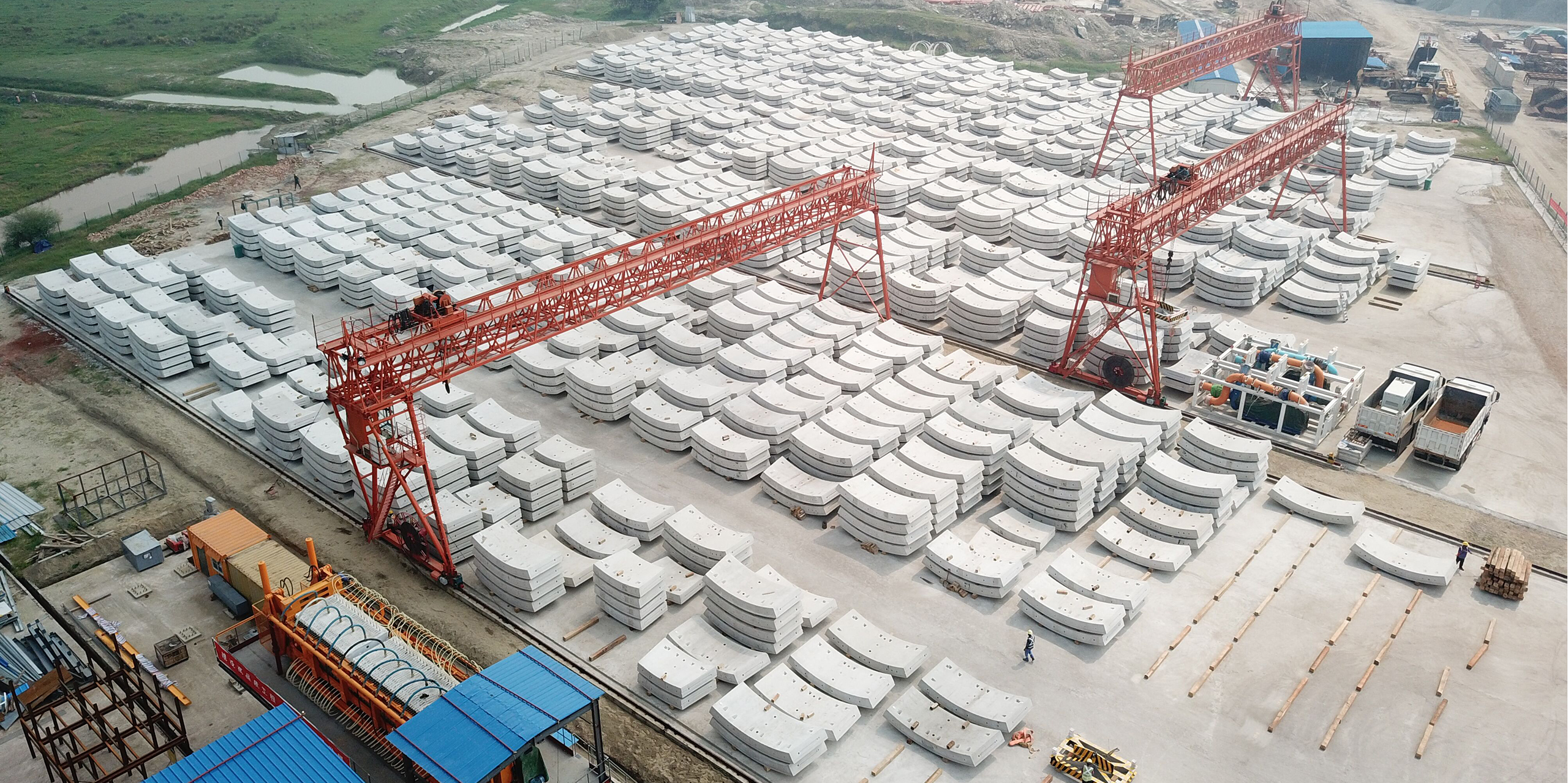


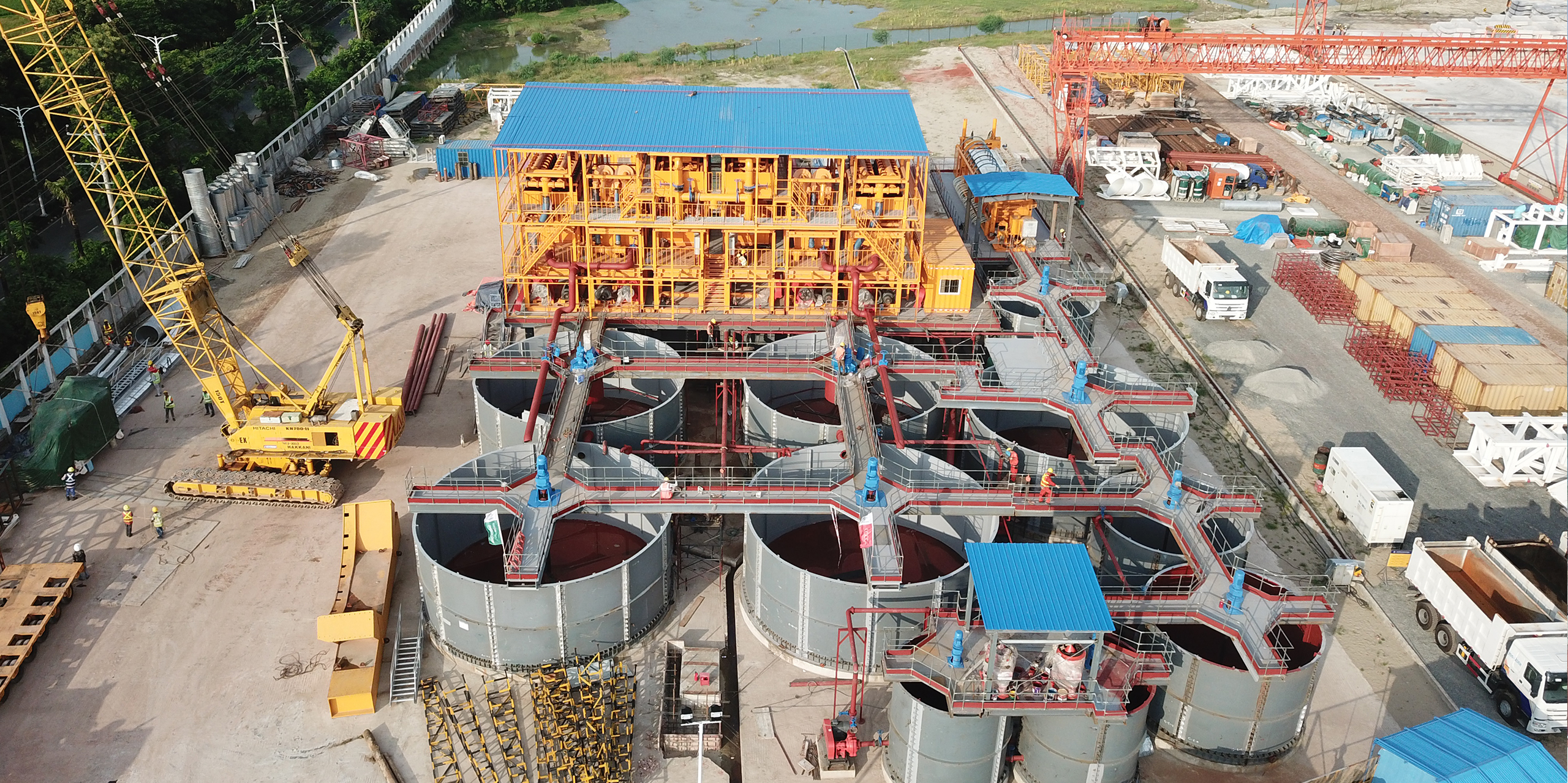
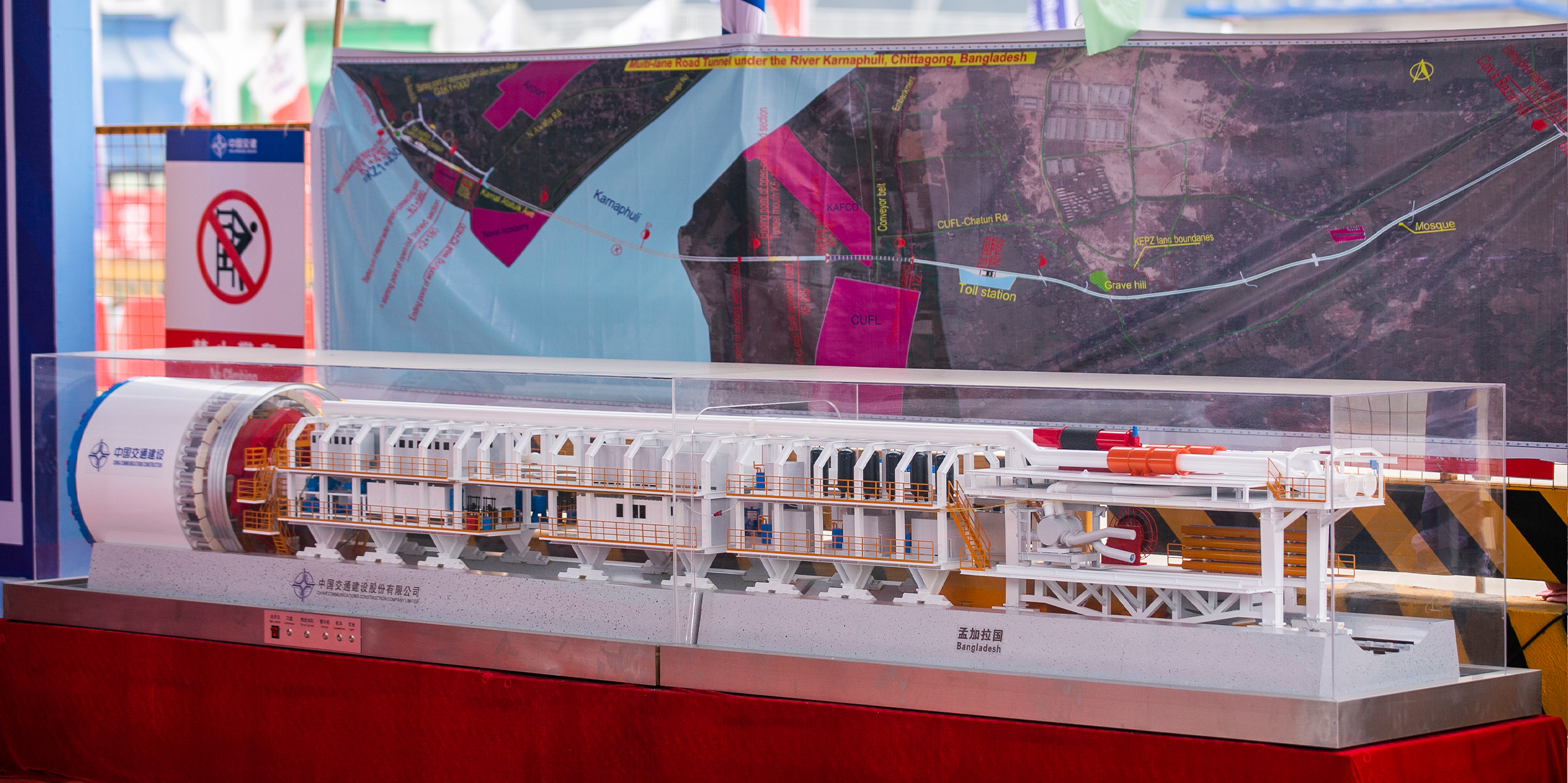
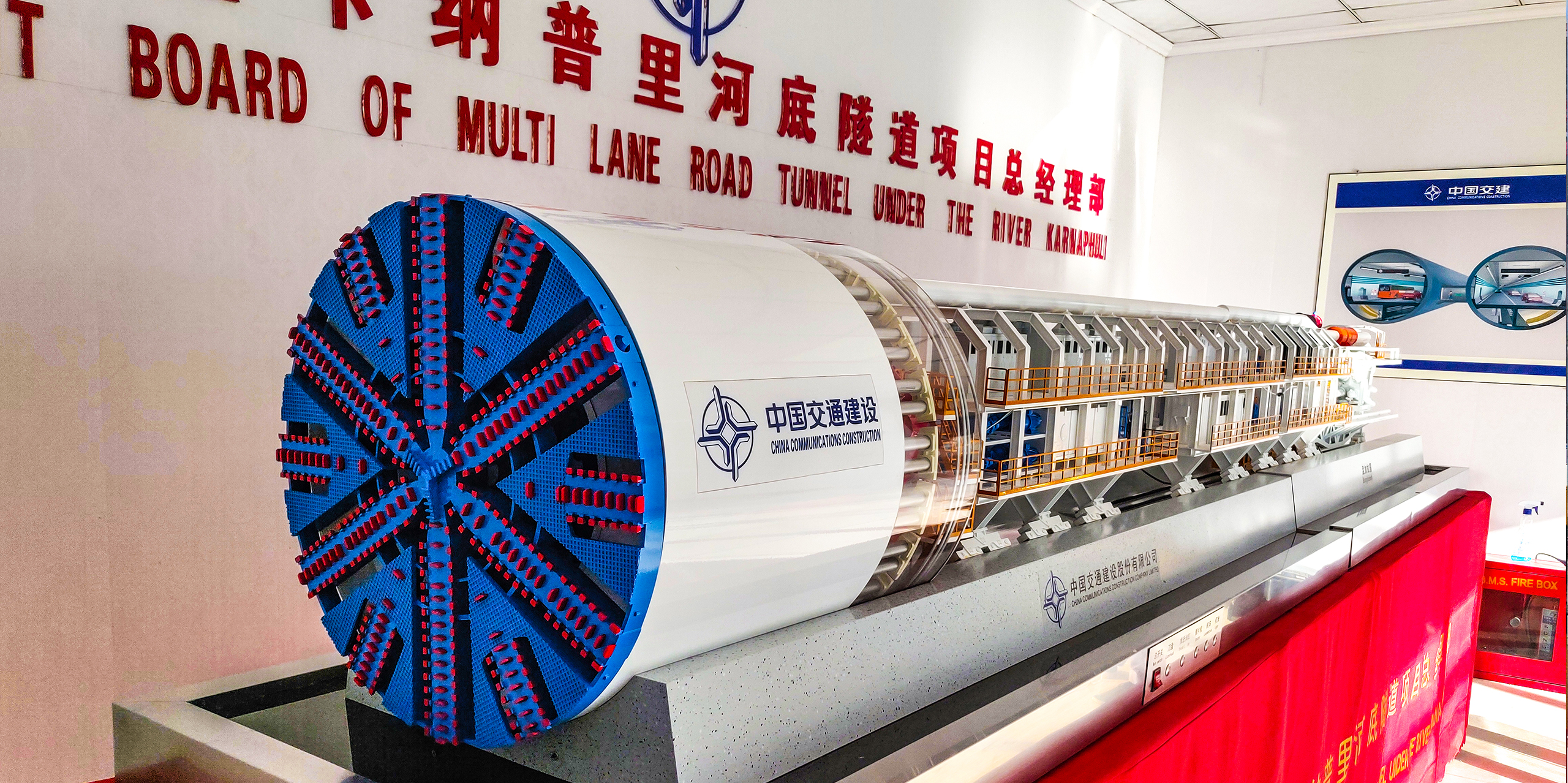

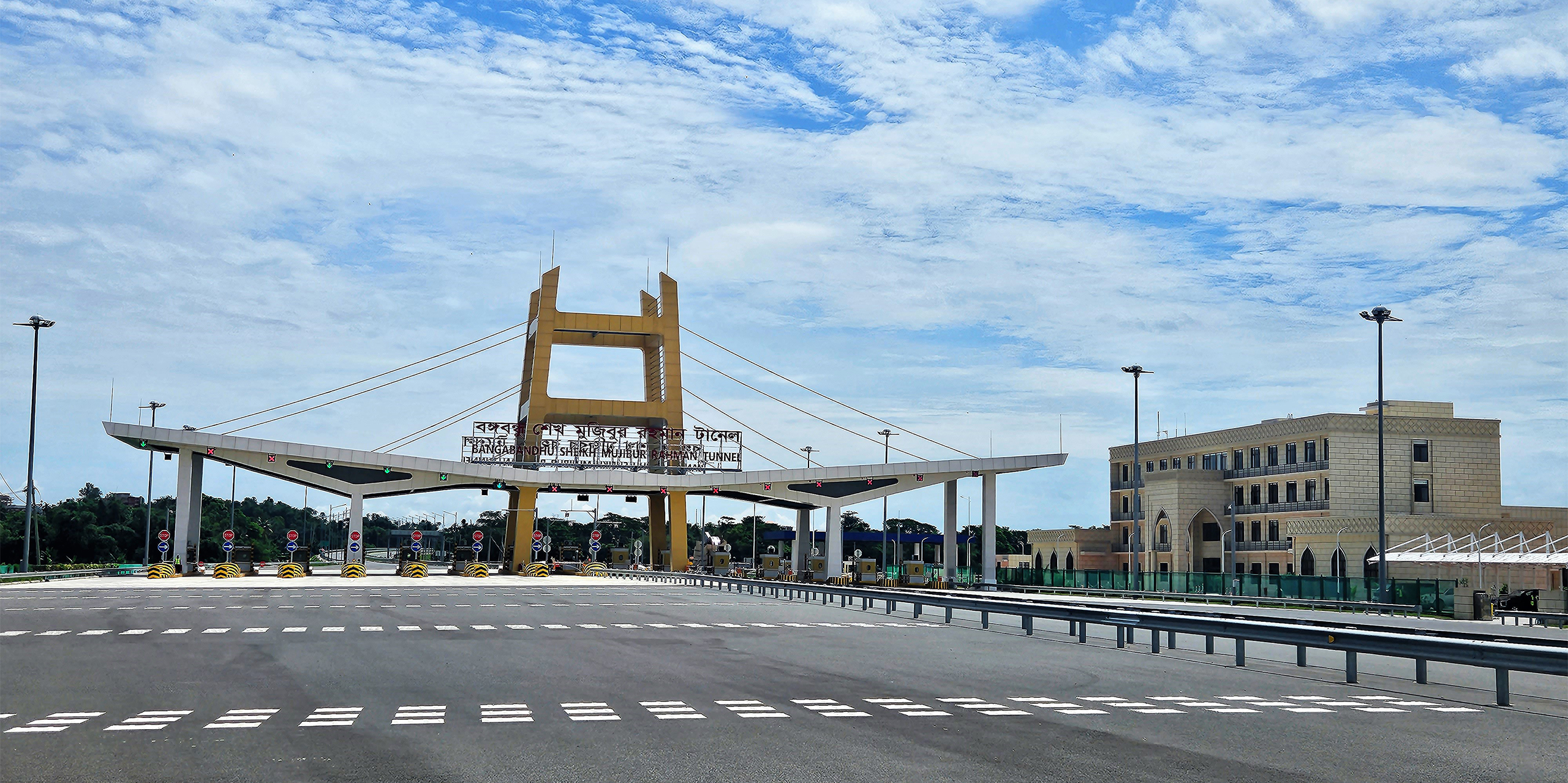
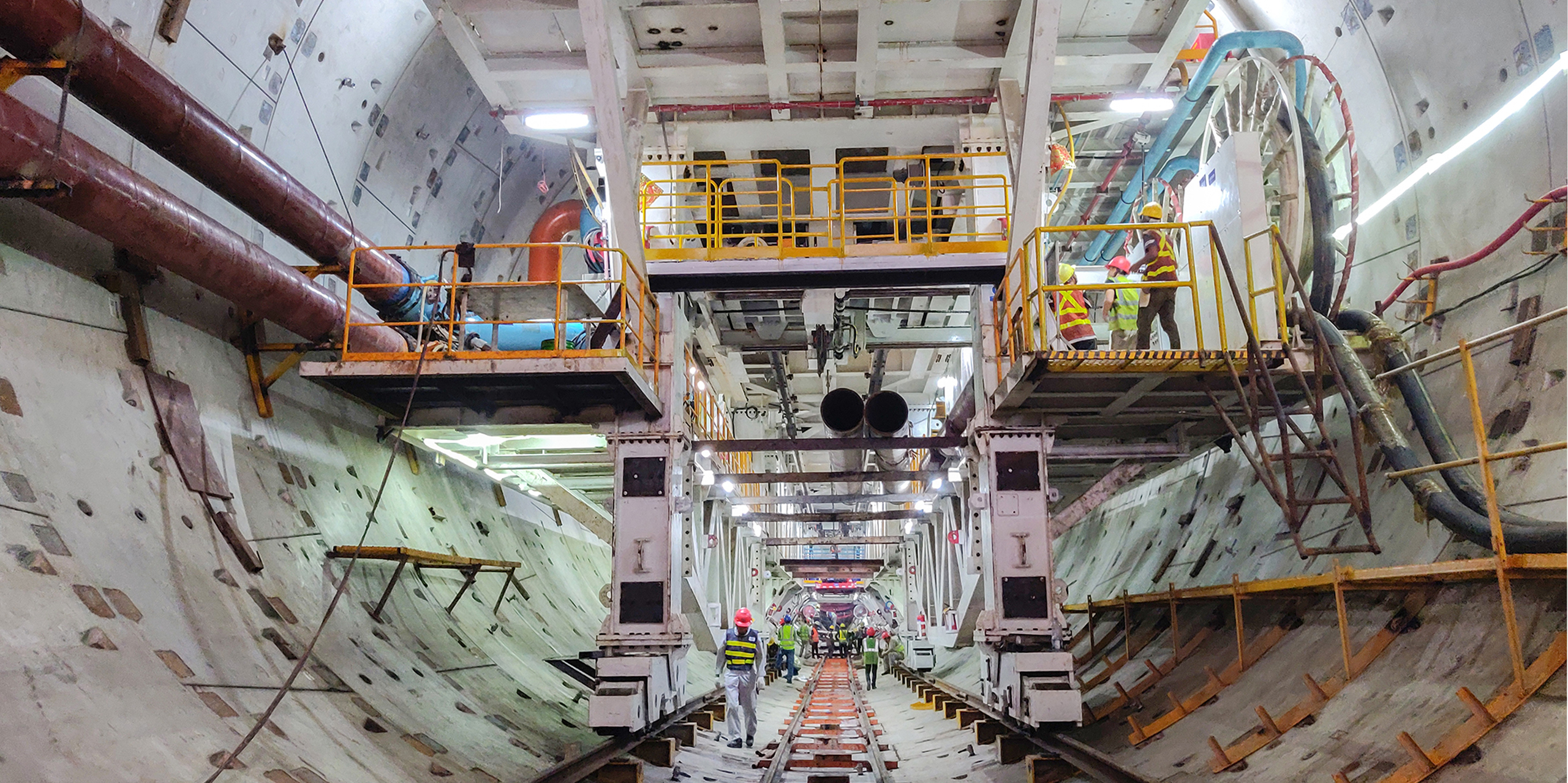
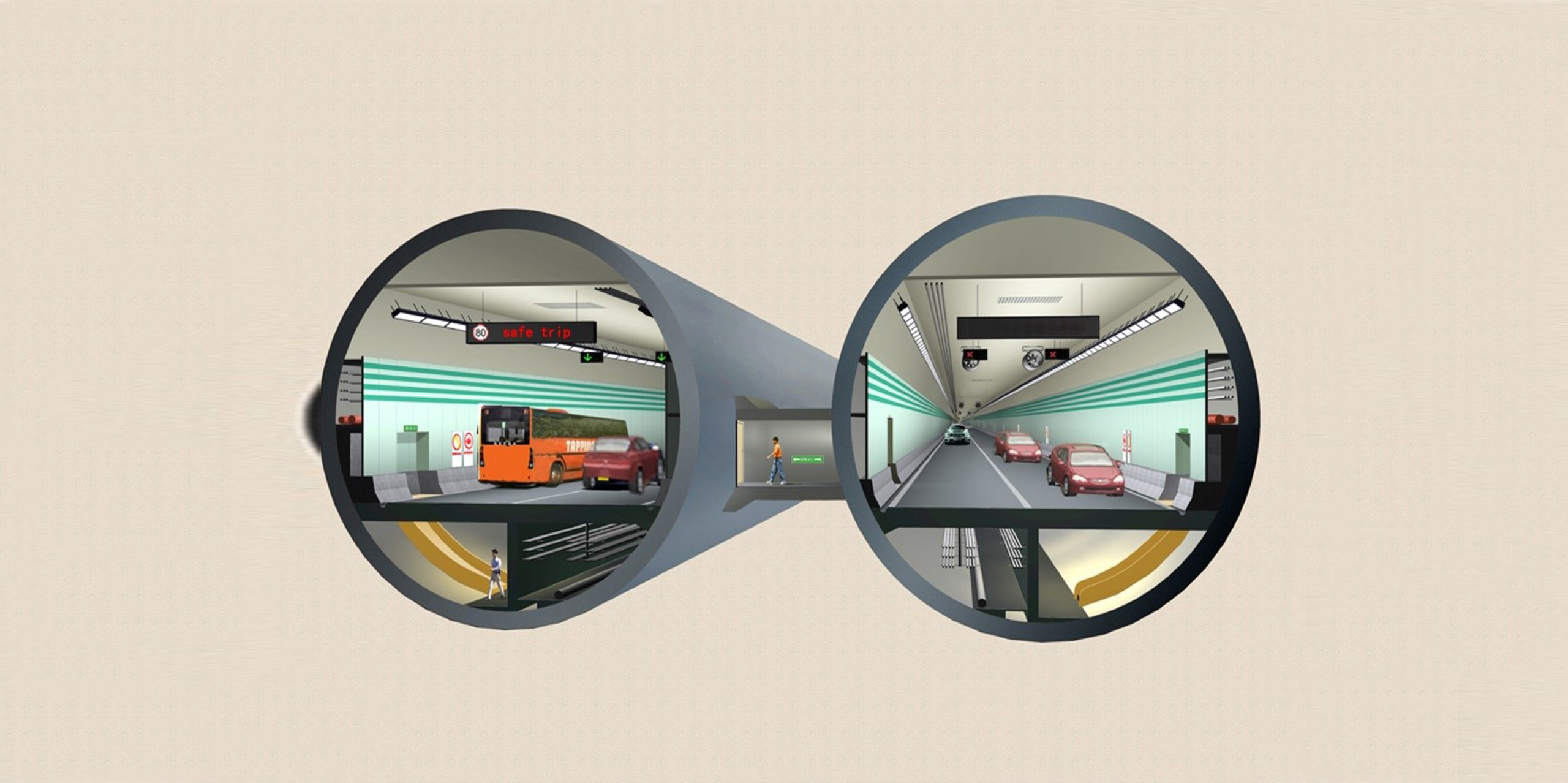
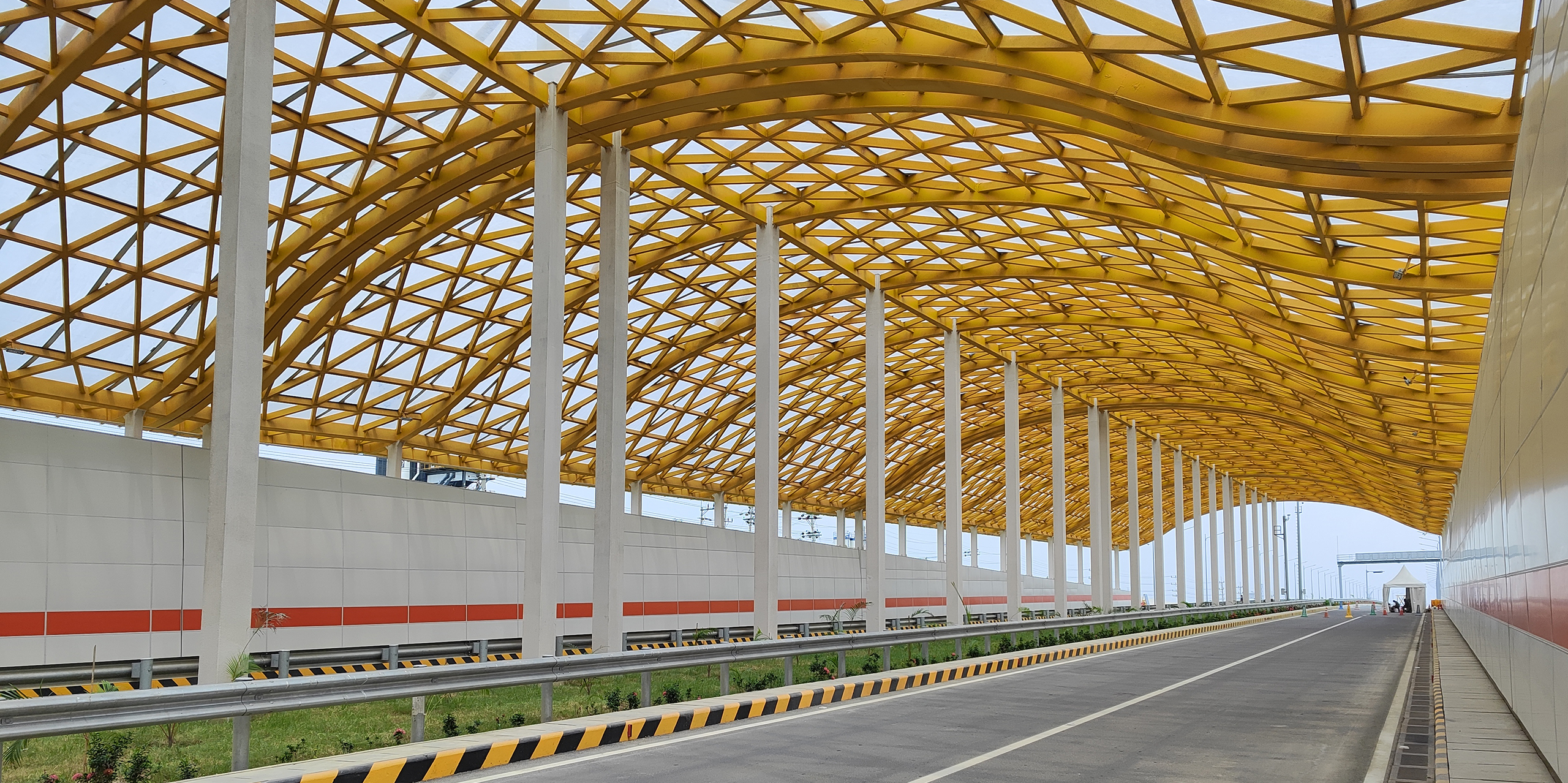


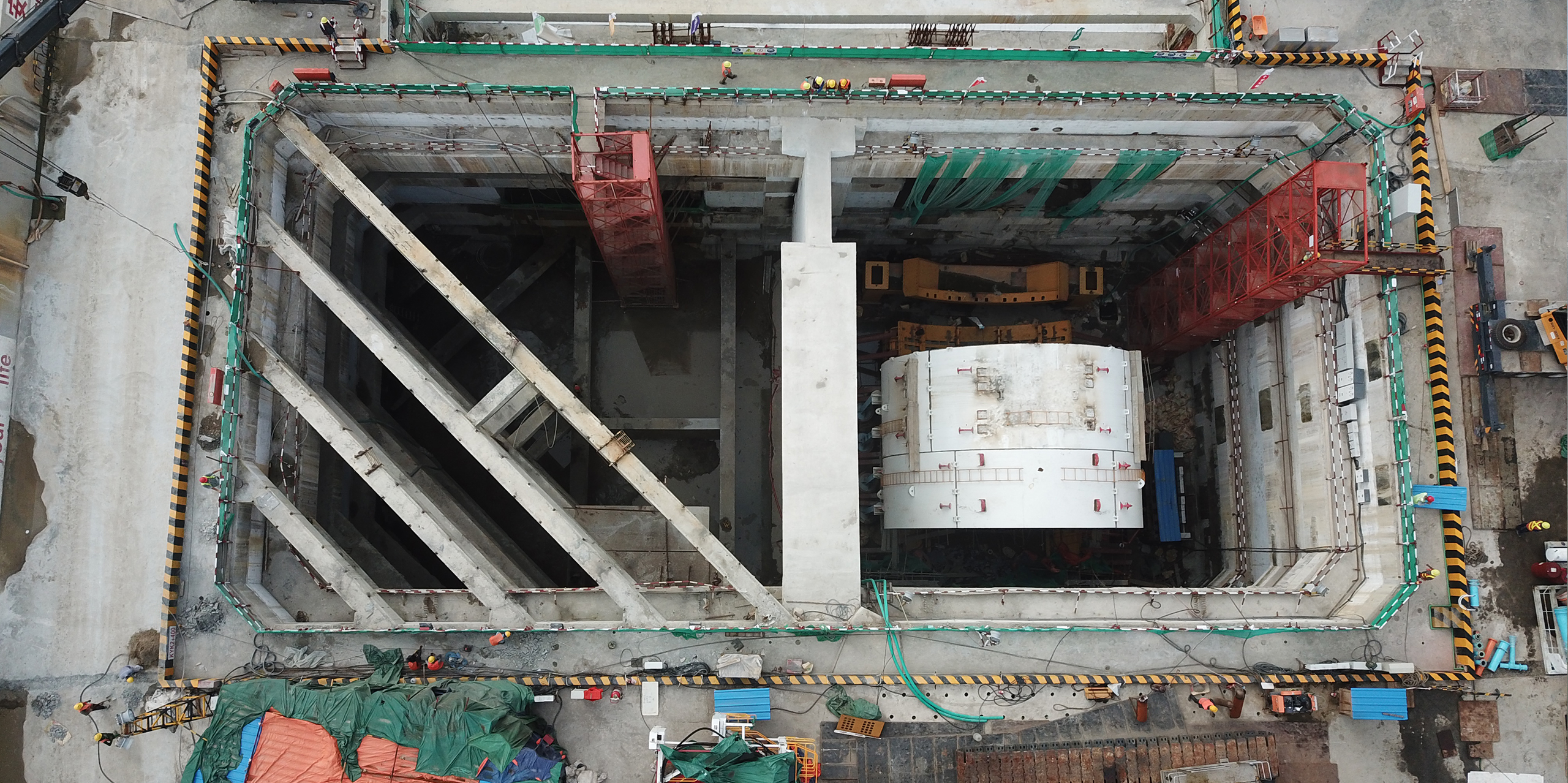
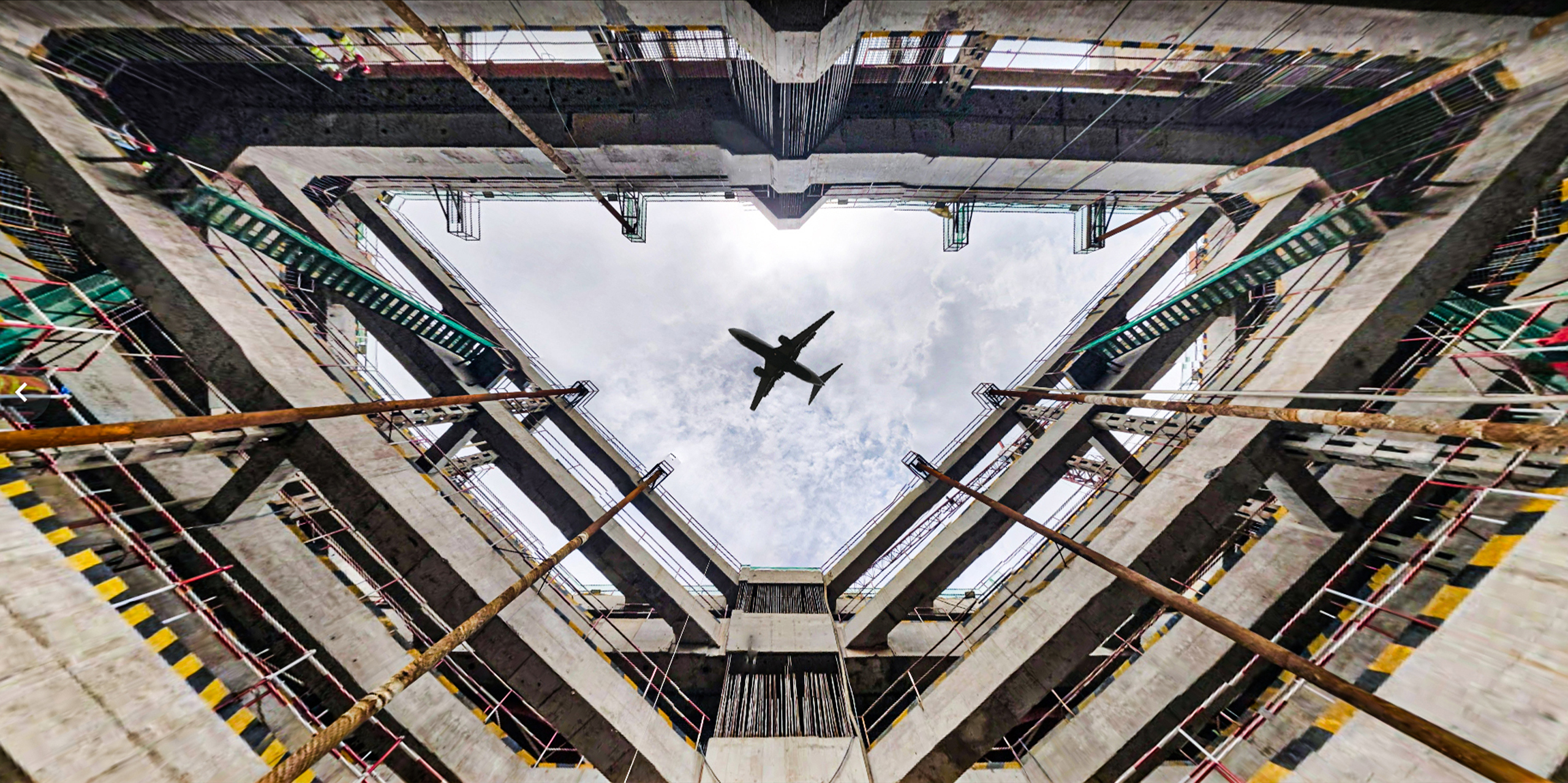
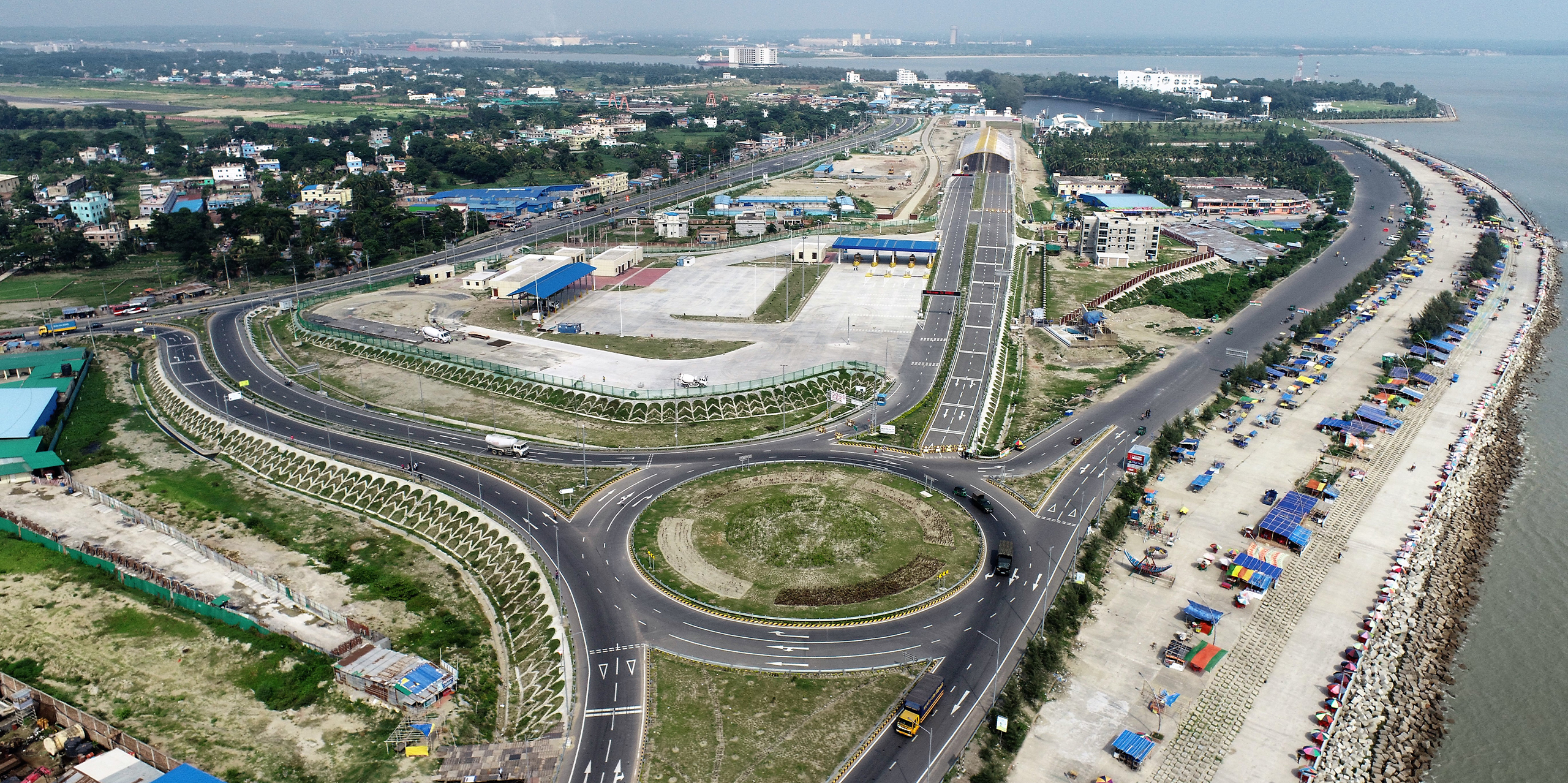

