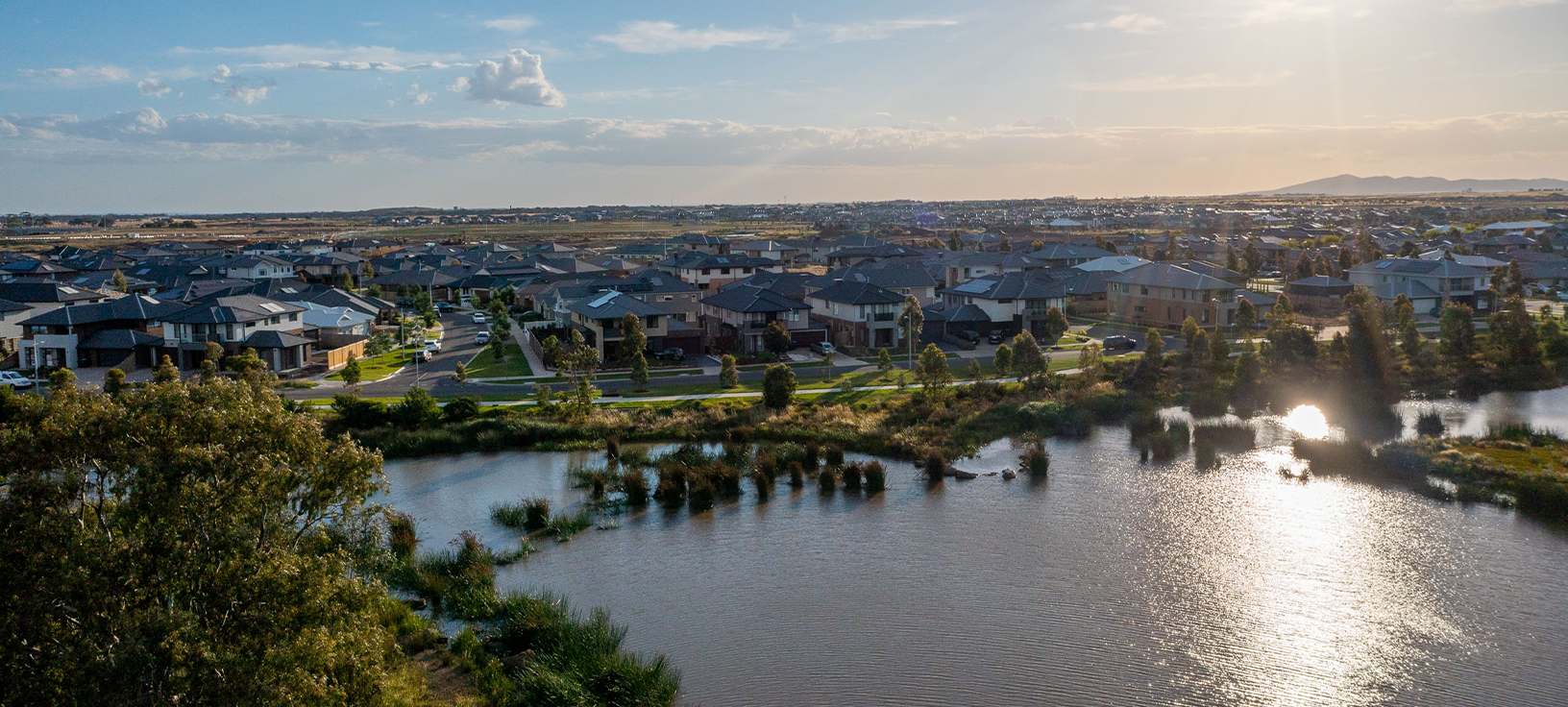
As manager of SMEC’s Property Advisory team, with over 20 years’ experience in the Urban Development industry, I have seen the ebbs and flows of land development and in my opinion land development has never been so challenging. Looking back at ‘the good old days’ it was relatively easy to navigate through the planning, design, and construction, however, today we are faced with multiple challenges and layer upon layer of regulations and procedures. The administration burden on projects is enormous and construction programs have ballooned; not long ago the average construction program was around 25 weeks, today we face 35+ weeks. The land development market is facing multiple external challenges, these include:
- Apprehensive end purchasers on the back of several large reputable builders falling into liquidation.
- Interest rates increasing to levels last seen in 2012 with the cash rate most recently lifting to 4.1%. That is 12 increases in the past 13 months.
- Authority requirements, standards, and land development constraints. The ‘red tape’ impact is stifling progress and adding another burden to development, land supply and the ability for developers to deliver feasible developments.
- The rapid rise in the Inflation Rate from 0% in June 2020 through to the current rate of around 7% which is well above the Reserve Bank of Australia’s 2-3% target rate.
- Competition for staff, materials, and plant due to numerous large local infrastructure projects.
- Additional fees and charges that are added to the developer’s feasibility models. The result being another blow to housing affordability when these costs are passed on down the line to end purchasers.
- Elongated construction timeframes resulting from workforce shortages, supply chain and resourcing issues combined with a reluctance for authorities to allow contractors and consultants to provide onsite workable solutions.
And, most topical today…
Civil construction costs increasing at unprecedented levels
Construction Cost Trends
To assist our clients in understanding construction cost movement SMEC’s Urban Communities team have tracked the construction costs over multiple stages within some of our key master planned communities since 2018. The methodology adopted was to apply construction rates from some of our major master planned community projects from key growth areas throughout Victoria to a set standard ‘typical’ schedule of quantities. This schedule captured all elements of a conventional stage within a large residential greenfield development to provide an accurate indication of the likely construction costs.
Construction costs within the land development industry have been escalating at unprecedented levels over the last couple of years. This is a result of numerous factors including:
- Record lot sales resulting from Government stimulus namely the Home Builder Grant and the requirement to deliver these lots.
- Impact of the infrastructure boom and unprecedented levels of State Government funded infrastructure projects has impacted supply chains, availability and cost of materials and labour.
- General price volatility resulting from ongoing issues; especially with risks around the cost of fuel and but also other petroleum related items like PVC Pipes.
- Ongoing supply chain issues resulting from COVID19 delays and isolations.
- Continuous increases in fuel cost because of uncertain global economic conditions, driving up costs throughout the entire supply chain.
- Recent wet weather impacting construction programs due to:
- Contractor availability and site requirements including dewatering and rework.
- Closure of tip facilities and requirement for contractors to stockpile on site and double handle material.
- Closure of quarries impacting the availability of quarry products and generally impacting the availability and access to products.
Research findings
The results of our investigations into civil construction cost trends since early 2018 associated with Victorian urban greenfield development are detailed below.
CONSTRUCTION COSTS – ACCUMULATIVE CHANGE |
|||||||
Q2 2018 | Q2 2019 | Q2 2020 | Q2 2021 | Q1 2022 | Q3 2022 | Q1 2023 | |
Overall | 100.0% | 110.3% | 106.4% | 110.2% | 118.2% | 131.0% | 146.8% |
Road & Drainage | 100.0% | 102.8% | 100.0% | 103.6% | 110.0% | 123.2% | 139.6% |
Sewer | 100.0% | 119.6% | 108.3% | 114.3% | 120.7% | 133.6% | 146.4% |
Potable Water | 100.0% | 107.6% | 105.9% | 106.2% | 118.3% | 128.9% | 137.8% |
Recycled Water | 100.0% | 108.0% | 106.3% | 106.9% | 118.3% | 130.7% | 139.3% |
Our research concluded:
- Overall civil construction costs increased by 46.8% between Q2-2018 and Q1-2023.
- At the commencement of the COVID-19 pandemic there was a small decline in construction costs, however, this did not persist and by mid-2021 costs had returned to pre pandemic levels.
- Between mid-2021 and the start of 2023 construction costs have risen sharply, approximately 37% in around 18 months.
- Over the review period, sewer construction costs increased around 47%. Sewer was also the most volatile element jumping almost 20% between mid-2018 and mid-2019 and then declining around 11% followed by consistent increases thereafter.
- The key elements impacting construction costs include:
- Fuel Price: Impacting running costs on site, particularly during bulk earthworks. Suppliers are also unable to absorb the additional fuel / transport costs and are required to pass these directly onto contractors.
- Quarry Products: Pressure on quarries due to unprecedented levels of development and building activity combined with operating restrictions.
- Precast Concrete: Record demand combined with the retreat from market from Rocla, have resulted in supply constraints. Some common concrete pipe sizes now have a lead time of around 35 weeks.
- Road Construction: High demand for materials and cost of manufacturing and transporting components. In 2022 the price of bitumen increased 26%.
- Copper: The price of copper has doubled in the past three years. This cost increase together with supply delays from overseas directly impacts electrical costs.
- Oil Products: Price of oil has been volatile because of global pressures and Australia’s reliance on overseas supply. General transportation and manufacturing of plastics elements such as plastic pipe and associated fittings are directly impacted.
The Grove Community
Our Outlook
Based on our research and significant interaction with major Victorian green field development projects and associated construction contracts, we have just started to see some softening of construction costs. This softening is occurring from a record high base and only associated with limited factors such as the slowing of lot sales and delivery of contracts associated with the home builder stimulus. However, we are still faced with multiple challenges, and believe rates will continue to rise, albeit, at a slower rate than what has been experienced most recently.
“So, what do I put in my feasibility model?” I hear you say…
Our opinion is that costs for the balance of 2023 will increase at a rate more reflective of inflation (plus some contingency), say 10%. Moving into 2024 and based on some of the influences explored in this article subsiding, we see costs weakening to sit around a more typical 5% increase. Post 2024 the government is endeavouring to tame inflation back to the target 2-3% and for the sake of the land development market we hope that construction costs follow this trend.
Atherstone community
What can be done now to lessen the impact in the current market?
SMEC’s Urban Communities team work closely with our clients and project stakeholders to help lessen the impact and exposure to construction cost increases and supply issues. Some of the strategies we recommend include:
- Consider large bulk earthwork packages, over multiple stages, to utilise large plant and provide onsite efficiencies by placing site won soil over large areas.
- Where possible consider the timing of construction activities, in particular the bulk earthworks component, targeting the drier months of the year.
- Pre-order materials that are currently experiencing long lead times such as concrete pipes, electrical substations, and PVC products.
- Investigate material substitutes, the use of materials that are non ‘standard’ such as polypropylene (plastic) drainage pipes. Some councils are permitting the use of plastic pipe in certain circumstances which can assist in shortening construction programs
- Explore the size of stages and the efficiencies of delivering larger stages.
- Where possible seek tenders / pricing from contractors on approved plans, therefore, avoiding the “tender to construction” variation and any opportunities to reprice construction elements. Where tenders are provided on unapproved plans seek pricing of all standard schedule items, therefore locking in the rates at the time of tender.
- Consider obtaining and utilising recycled material from the project site such as earthworks or rock. Explore any project efficiencies (time and cost) of a rock crusher or if you have multiple sites within close proximity consider reusing materials between sites, this can avoid tipping fees and reduce environmental impact.
- Work with your design team and examine the site conditions to ensure that the most efficient design is being considered. At SMEC, we utilise our inhouse Geotechnical team to undertake seismic modelling to map the extent and depth of ‘hard rock’ throughout projects. This enabled us to design around areas of significant rock, which mitigated the need for extensive and expensive rock removal and earthworks.
- Challenge the authorities with respect to the most efficient design or present opportunities to improve “the norm”. Is it necessary to have a footpath on both sides of a minor local road?
- Consider the end user and their requirements. Does the builder require a (near) flat allotment, or can we design to their maximum fall to reduce earthworks while still achieving the same result?
- Spend time undertaking extensive master planning to ensure the most efficient design over the entire project site.
- Work with suppliers to understand the supply constraints and where possible tweak designs to avoid elements that have long lead times or are challenging in the current environment.
- Keep your civil contractor informed on the development progress and explore areas where efficiencies can be explored.
Contact Nathan to connect with SMEC’s Urban Communities property advisory team.
About the Author
Nathan is Manager of the Property Advisory team within the Urban Communities business and has over 20 years’ of urban development experience delivering projects and advice to the land development industry. A member of the Property Council of Australia’s Residential Developers Committee since 2018, Nathan is respected by his peers and clients and prides himself on delivering accurate and timely advice as a trusted advisor to the industry.
The SMEC Property Advisory Team is a specialist arm within the Urban Communities Business, focussing on property investigation, acquisition, divestment and feasibility assessments. Our dedicated team leverages from our highly experienced multi-disciplinary development experts to provide trusted advice to the land development industry.
Our whole of project approach combined with our respected relationships with Authorities enable timely and accurate advice. Our broader real estate contacts and partners place SMEC at the forefront of market opportunities and with access to skilled resources from varied disciplines and combining this with over 50 years of industry experience, SMEC is your trusted advisor.
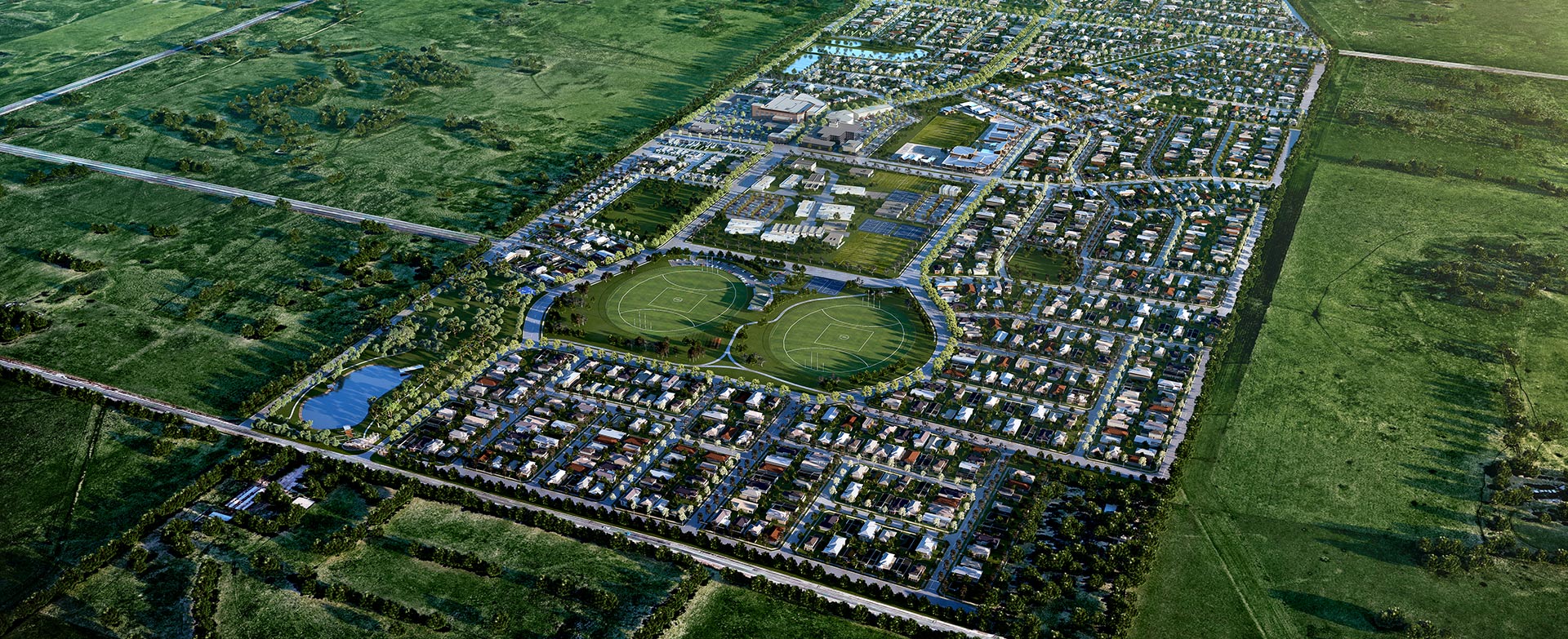
Urban development has changed dramatically over the past 20 years and future transformation will continue to occur swiftly. At SMEC, we are preparing for seismic shifts in urban development practices that could potentially rewrite how we design the spaces in which we live and work.
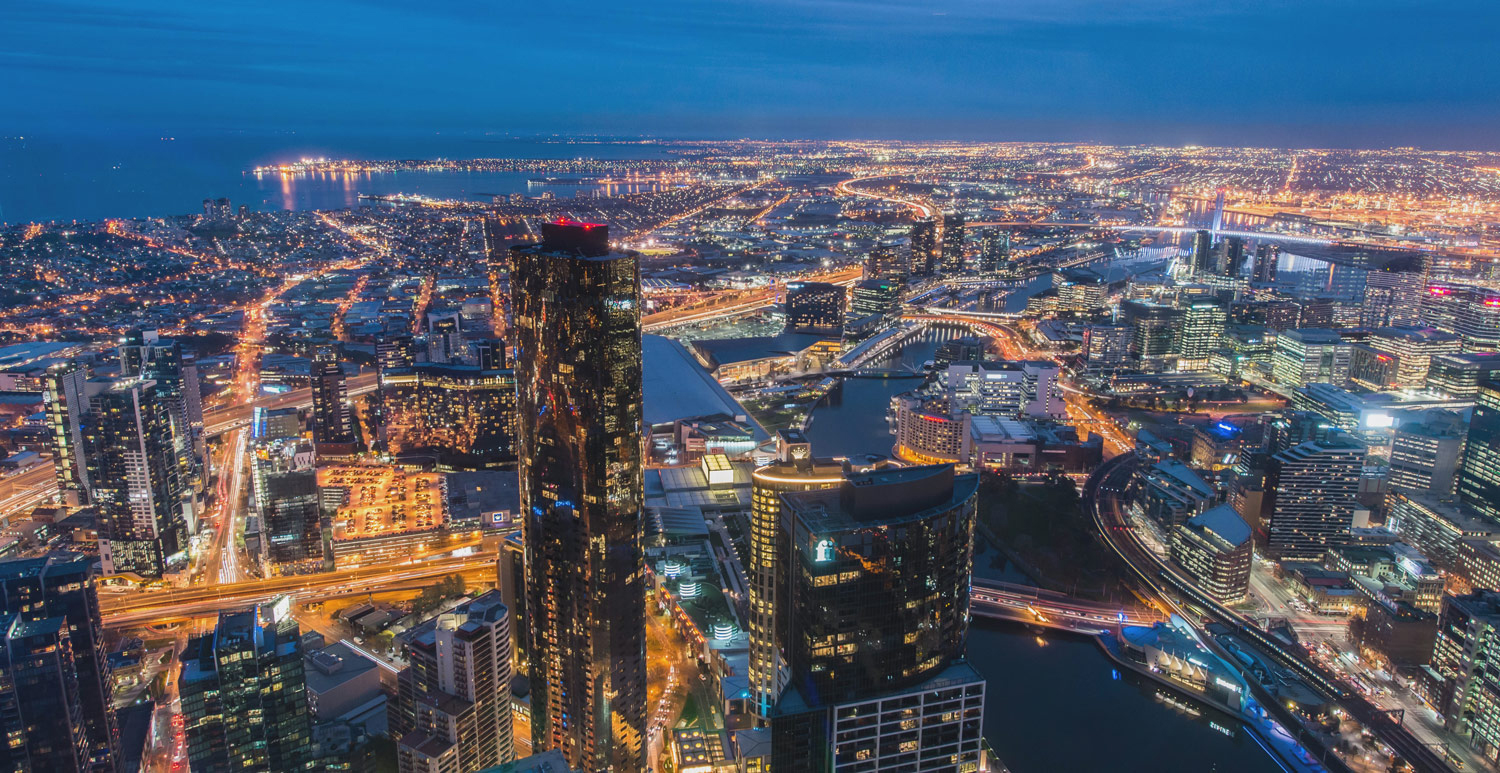
SMEC is made up of problem solvers. We have always helped to find solutions for people - it’s part of our DNA. That’s why the Smart Cities agenda simply represents a contemporary part of our innovation journey and fits neatly into SMEC’s strategic approach to grow and diversify our business.